Si deseas leer este Post, relájate,
date tu tiempo, Abre tu Mente y analízalo bien. Cada día se hace más evidente que
los avances acelerados en el almacenamiento y procesamiento de información, tanto
a nivel Hardware y Software, y las tendencias que la competitividad por los mercados
ha marcado sobre Industria 4.0 y la Internet Industrial de las Cosas (IIoT) que
estarán materializando el Parte aguas que se dio en 1950 con el nacimiento del Mantenimiento
Productivo, esto es enfocar el trabajo de
mantenimiento a obtener la calidad y cantidad de producto y no solo al cuidado de
las máquinas (Mantenimiento Preventivo) que hasta aquellas fechas prevalecía como
medida idónea en las fabricas.
Debido a los trabajos de Taylor en
la aplicación de tiempos y movimientos, creció el interés por el uso de la estadística
en el trabajo pero su aplicación era muy lenta y poco confiable. Walter A Shewhart
(1891- 1967) desarrolla la idea del Control Estadístico de Calidad (SQC siglas en inglés) y Deming se le une para aplicar éste a
la industria norteamericana lo que estuvieron haciendo hasta la llegada de la II
Guerra Mundial. Los triunfos comprobados por el uso de la estadística en la industria, norteamericana hacen que esta acepte su uso regular
y Shewart presenta su libro en 1931 “El Control
Económico de la Calidad del Producto Manufacturado” (The Económic Control of Quality
of Manufactured Product).”. Aquí nace el concepto de los Limites de Control de Proceso
y se hace hincapié en la existencia de eventos que al estar dentro de esos limites
(tolerancia) se les llama Causas Comunes y a los que se presentan por arriba y por
abajo de los mismos se le llama Causas Especiales. Esto lo expuse hace décadas ( Segundo Congreso Nacional de Mantenimiento Octubre 22 de 1990, Asociacion Mexicana de Mantenimiento) y que la interpretación de la información estadística de como marcha el Proceso nos ayuda a distinguir entre las Causas Comunes y las Especiales que afectan a la Calidad
En los siguientes diagramas de Control de
Proceso, Uds. pueden ver ¨Lo que
Hace la Maquina y No él Como es la Maquina¨. Desde aquí nace y se
percibe la idea correcta del concepto de lo que debe ser el significado del
Mantenimiento. Lo importante de las maquinas, equipos, infraestructura es la
Calidad de lo que hacen, esa es su Razón de Existir, de Ser.
De tal suerte que el verdadero
concepto de los que es el Mantenimiento Correctivo y el Mantenimiento Preventivo
queda rebelado
Y su conformación con respecto a
los defectos y las fallas queda clarificado, evitando con esto las múltiples
fricciones entre el personal que ofrece un servicio y el que lo recibe, pues
estan Armonizados y Alineados los conceptos de ambos puntos de vista
La rapidez de los procesos de innovación
tecnológica y la lucha por conquistar los mercados, junto a la gran dificultad
de incrementar el la eficacia para asegurar cuando va a presentarse una falla
con las graves pérdidas y consecuencia que conlleva, así como la miniaturización
y disminución del costo de sensores y aumento dramático del almacenamiento de
datos, nos permite hoy en día ver con más claridad que sin duda, el haber
centrado y girado el concepto del Mantenimiento y alrededor de la Maquina no fue ni lo
correcto, ni lo efectivo y si nos provoco muchos problemas de entendimiento, que convergen en una baja
productividad en las empresas de todo tipo de giro comercial e industrial.
El problema siempre radico en confundir e intercambiar los
conceptos, dándole al Mantenimiento (visto actualmente como arreglo de
maquinas) la función que es propia de la
Conservación Industrial (Mantenimiento + Preservación) y que esta con este nuevo
marco armonizado, muestra que ella esta subdividida en dos ramas, una llamada
la Preservación que ve la parte Física del Activo y la otra el verdadero Mantenimiento
que vela por el Nivel de Calidad Estipulado del Servicio que provee la maquina,
y que visto con esta óptica de Teoría General de Sistemas, nos muestra que en
nuestro presente y más fuertemente en el Futuro Próximo, los fabricantes de los
Activos serán los responsables del Cuidado de las Maquinas como nicho fortalecido de su mercado y que
por tanto tendera a desaparecer sino
no es que a minimizarse la función de cuidado a la maquina, pues mucha de ellas
inclusive aumentara dramáticamente su cualidad (Sin Preservación dentro del
Periodo de Garantía) impulsada por esos datos que el Big Data en la nube analíticamente
manejara. En cambio el Nuevo Paradigma que se perfila la los equipos es Garantizar la Capacidad de Producción y no
tanto la rata de fallas.
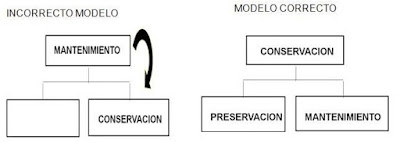
Esto Obliga actualmente a Diferenciar
las Labores que están encaminadas hacia la Salud del Equipo (Preservación) y aquellas
encaminadas a sostener el Nivel de Calidad producido por el Activo (Mantenimiento)
y puesto que son las actividades de sostenimiento
del Nivel de la Calidad lo que conserva la Supervivencia de las Empresas en el actual
mundo globalizado y competitivo, esta característica de la Calidad creara todas
las corrientes del conocimiento técnico y científico necesarias para su desarrollo
y permanencia aun, por sobre las actividades de Preservación (parte Física), ya
que estas reflejan que los Activos presentan patrones de falla que tienen mucho que ver con el Azar y
que realmente solo a través de un Monitoreo
Continuo de características operativas de los Activos tales como vibración,
temperatura, presión, demanda de corriente y voltaje, etc . podremos mediante sensores
diversos interconectados en línea con el proceso, el cliente, los proveedores
de partes OEM y la analítica de grandes bases de datos con poderosos software
especializados de estadística, probabilidad y riesgo, predecir con mayor probabilidad las fallas en los equipos, técnica
que hoy se denomina Prescriptivo.