MANTENIMIENTO VISTO COMO UN NEGOCIO
Por Ing. Carlos López De León
Estudiando la economía de las empresas de Standard&Poor´s 500, se puede ver que el 80% de su valor no puede explicarse en sus balances. Lo que es posible explicar con ellos son los activos tangibles. Así, sólo el 20% del valor puede rastrearse hasta los activos tangibles, el 80% es intangible.
Entonces cuales son los activos intangibles de los que estamos trabajando?.Son el Conocimiento, las Competencias de las personas, la tecnología de información, las marcas, es decir aquellas cosas críticas que sirven para crear valor.
Un estudio realizado por Earnst & Young en 1998 analizó la forma en que los inversores profesionales valuaban a las empresas. De ese estudio se desprenden los primeros 3 lugares, a saber:
Primero es la Capacidad para ejecutar la Estrategia.
Segundo es la confianza en el equipo ejecutivo.
Tercero es aquella que menciona la calidad de la Estrategia. Se le llama estrategia a aquellas acciones que se desarrollan en cualquier momento para obtener resultados futuros. La estrategia es la forma en que una organización se propone crear valor.
Hablamos del Principio de Pareto en la Administración del Mantenimiento Industrial porque nos permite estimar que el 20 % de los Activos provocan el 80 % de los problemas que influyen en la productividad de la empresa y que el restante 80% de los equipos solo repercute en un 20%. Entonces la pregunta que nos debemos hacer es ¿qué estamos haciendo en nuestras empresas para manejar este control de riesgos a fin de dar mejores resultados en la competitividad del País?
Resulta curioso saber que el Gross Domestic Product (GDP) o también conocido como Producto Interno Bruto (PIB) mundial en el 2009 fue de $ 60,587 (millones de dólares) y que de este valor, la función de mantenimiento equivale al 9% aproximadamente 5,452 (millones de dólares) a nivel mundial. Esta es una cantidad muy grande y debería ser más tomado en cuenta. A nivel nacional del año 2004 según datos del INEGI, en México se gastaron $42,715 millones de pesos en el rubro de pagos por reparaciones y refacciones para mantenimiento corriente.
Estamos entonces ante la función de Mantenimiento que debe ser visto como un Negocio, y que resulta ser un área de oportunidad que nos representa un impacto muy significativo en la solución a la competitividad de nuestros Países, sobre todo si entendemos que algunas direcciones de planta:
1. No tiene la Capacidad para ejecutar la estrategia de Mantenimiento.
2. No cuentan con la confianza en el equipo ejecutivo de mantenimiento
3. La gerencia de mantenimiento no cuenta con una calidad de su estrategia de mantenimiento.
Recordemos que según el IMCO (Instituto Mexicano para la Competitividad) la competitividad es la capacidad de un País para atraer y retener inversiones. En el área de la administración de activos físicos, creo es conveniente mencionar que la baja productividad encontrada, tiene también a las deficiencias del mantenimiento industrial como un factor común, y más en su falta de estrategia y táctica alineada y armonizada con la visión y misión del negocio.
Si estamos de acuerdo con la pirámide que contempla a las ventajas competitivas hasta arriba, en medio a las ventajas estratégicas y en la base los activos estratégicos lo podremos comprender con más claridad. (Vision Daryl Mather)
Entendemos por Ventajas Competitivas, Las habilidades y capacidades para tener mejor rendimiento que nuestra competencia.
Por Ventajas Estratégicas, el grupo de recursos y habilidades que son difíciles de imitar, raros y especializados que contribuyen a la ventajas competitivas de la empresa.
Y finalmente por Activos Estratégicos, los recursos y habilidades necesarios para crear las ventajas estratégicas.
Este marco, sugiere ahora la importancia de armonizar y alinear la función de la administración del mantenimiento industrial.
La administración del mantenimiento industrial es el área que ha tenido mayores cambios en los últimos 10 años. Estos cambios en las direcciones de planta, de nuestras empresas aun no han permeado significativamente.
Por ejemplo continuamos teniendo como un importante Kpis los tiempos muertos de los equipos con la connotación de horas improductivas, siendo que ese paradigma cambio con la Ley Sarbanes al siguiente “Atentar contra el inversor a su derecho a obtener utilidades” lo que está a su vez alineado con una de las acepciones de la competitividad definida como la ¨Capacidad de atraer y retener la Inversión¨ como se mencionó anteriormente.
Mientras no se armonice esta función y se le dé su contexto correcto dentro de la alta estrategia del negocio, permaneceremos con bajos índices de desempeño.
COMO REDUCIR EL GASTO DE MANTENIMIENTO EN ESTOS TIEMPOS
La administración de los costos en estos tiempos de crisis económica, se ha vuelto un factor crítico dentro de la gerencia de activos físicos. Al punto que los expertos Directores de Planta vislumbran que la misma supervivencia de una compañía podría depender bien de su habilidad de contener estos gastos, en el corto plazo siempre y cuando no se sacrifique la viabilidad en el largo plazo.
Desgraciadamente, cuando los tiempos se ponen difíciles, a veces la solo táctica y el nerviosismo natural provoca una disminución no racional del gasto de mantenimiento. Lo importante es que esta época, es una Oportunidad de mejora significativa y que puede provocar un fortalecimiento de la empresa para remontar airosa en el corto y largo plazo
El truco radica en disminuir los gastos de mantenimiento racionalmente y paralelamente se debe mejorar la capacidad, productividad y rentabilidad simultáneamente, sin dañar la entrega o calidad. ¿Qué mejor oportunidad deseaba para formar y alinear su equipo de trabajo?
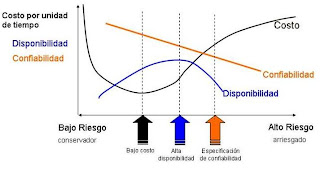
Curiosamente cuando la función de mantenimiento no se está manejando bien y en especial, lo que se conoce como mantenimiento preventivo programado. Se produce entonces la oportunidad de mejora de la que hemos hablado, ya que el Mantenimiento Preventivo (MP) es rico en oportunidades de mejorar.
Nuestra experiencia nos ha demostrado que no es raro encontrar programas de MP manejados pobremente en las plantas industriales. Y tal es el caso, que es frecuente encontrarse con este hallazgo ¨Más de la mitad de todo el trabajo de mantenimiento son innecesario¨ y que las prácticas del Mantenimiento Predictivo son ineficaces y costosas.
En qué basamos estas aseveraciones y que Ud., podrá comprobar en su medio industrial
• Los equipos, instalaciones y construcciones que están contenidos en los programas de mantenimiento preventivo NO FUERON INCLUIDOS EN ESTE, EN BASE A UNA CALIFICACION NUMERICA DEL RIEGO. Es decir los equipos que están en esos programas (y de los cuales se generan los gastos en refacciones y mano de obra de los cuales ahora tenemos que reducir motivados por la crisis) no fueron en primera instancia calificados en base a un estudio de criticidad dentro de un contexto operacional, esto es, están ahí porque mantenimiento así lo definió, sin tomar en cuenta a producción, ingeniería y finanzas.
• Los intervalos de los mantenimientos programados casi nunca se revisan dentro del contexto del ciclo de vida útil del mismo. Si acaso en sus inicios fueron establecidos conforme al fabricante, pocas veces se revisan sus frecuencias. Es decir éstas son hechas muy a menudo o demasiado tarde, lo usual que encontramos es muy a menudo.
• Los procedimientos del mantenimiento programado (si es que se tienen) tampoco se revisan con cierta frecuencia dejando muchas veces al arbitrio de quien lo ejecuta la extensidad e intensidad del mismo. La probabilidad de provocar errores humanos crece cuanto más extensiva e intensiva es el trabajo de mantenimiento. En otras palabras las descripciones de las tareas a ejecutar son inciertas, incompletas y malas.
Recordemos que la razón de ser de una actividad es la de agregar valor y en el caso del mantenimiento preventivo, muchas veces no agrega ningún valor. Los estudios y análisis del Mantenimiento Centrado en la Confiabilidad demuestran que por mucho o poco mantenimiento preventivo que se tenga, no se puede asegurar que la falla no se presentara (ver RCM2 por John Moubray)
Esta forma de manejar el mantenimiento preventivo luego entonces podría producir las siguientes aproximaciones
Solo utilice el 30% del mismo, es preferible inspeccionar, acercarse al operador y conjuntamente mantenimiento y producción ¨Tocar con la mente primero a la maquina y después con las manos¨.
Puede, después de hacer su estudio de criticalidad de equipos, borrar el 20% de sus mantenimientos programados. Pregúntese porque están ahí y si realmente funciono el tenerlos ahí. Seguro encontrara la respuesta ¨Siempre así se ha hecho, pero no encontrará razones¨.
Las 6 curvas de probabilidad de falla que se tienen en la actualidad, solo para un 11% se demostró, que las fallas tienen que ver con la vida de los elementos fallados y recuerde que precisamente es este el argumento en el que se basa el personal de mantenimiento para elaborar los programas de mantenimiento programado generalmente.
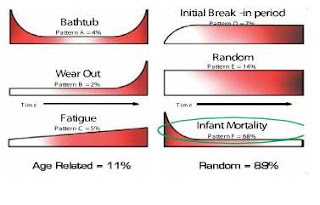
El restante porciento de las fallas nada tiene que ver con la edad de los elementos fallados.
Más concretamente el 11% relacionadas con la edad, el 68% de las fallas esta relacionado con el inicio de la funcion o vida del item y el restante 21% es al azar.
Por tanto podemos extender hasta más del 30% los intervalos de los tiempos de esos mantenimientos programados, ahorrando muchos miles de dólares con un bajo nivel de riesgo a equivocarnos.
Con esta nueva visión podremos disminuir sensiblemente los paros de equipos (puede encontrar que casi un 20% fue pérdida de tiempo y tal vez un 40% de horas extras innecesarias), así como los procesos de la adquisición de refacciones y toda la logística y flujo que con lleva.